DVP characteristic and application. Fiberboard (fiberboard)
Consider in this article one of the popular building materials that is used in construction finishing worksoh.
The abbreviation for fiberboard is translated as follows. Fibreboard.
What is fiberboard?
Fiberboards are good stuff for construction finishing works. Namely, they are suitable for works related to wall cladding, frame partitions, ceilings and are applicable for floors as a lining material for the required coating. This material is used not only in construction and finishing works, but also in other areas. Such as, automobile production, furniture production and production of various containers.
Types of fiberboard
According to the method of production and use of fibreboard, they are divided into the following types:
- Soft is used in construction and finishing works when they install sound and heat insulation systems. This type of fiberboard is used in this area because of its characteristics. This type has a very strong porosity and is not a durable material.
- Semi-hard has increased strength and can withstand heavy loads. Because of this, this vee is very well and successfully used in the furniture industry.
- Super-hard is a very high quality, load-resistant and high-density fiberboard. This type is easy to process, very easy to install and is suitable for construction work, namely for the installation of arches, flooring, doors and partitions.
- Refined fiberboard is a very well finished surface. These types of slabs are imitated under decorative tree different colors and shades. Dignity is, of course, a beautiful appearance.
Main dimensions (dimensions)
On average, the thickness of fiberboard sheets is from 2.5 mm. up to 40 mm. But there are also slabs of low and medium density, in which the thickness varies in sizes: 8, 12, 16 and 25 mm. Semi-hard fiberboard boards have a thickness of 6, 8 and 12 mm. Both hard and super hard materials are available in the following thicknesses: 2.5, 3.2, 4.5 and 6 mm.
Average in length varies from 1220 to 3000 mm, and in width - from 1220 to 1700 mm. And the maximum size that exists in nature is 6100 × 2140 mm. Naturally, fiberboard with such dimensions cannot be used for domestic purposes, but is more suitable for industrial applications.
Soft and hard board brands
Soft boards are marked with the following abbreviations:
Solid fiberboard plates have the following markings:
- T - hard with an untreated front layer;
- T-P - hard with a painted outer layer;
- Т-С - solid, with a lining of fine wood pulp;
- T-SP - solid, with a fine wood mass cladding and a painted outer layer;
- ST - superhard plates with an untreated outer layer;
- ST-S - super-hard slabs with a cladding of wood finely dispersed mass.
Pay attention to the fact that fiberboard plates of the TP, T-SP brands. TS and T are divided into groups: A and B.
According to the quality indicators of the surface treatment of fiberboard, plates of the same grades are divided into I and II grades.
Wood has long been considered one of the best building materials, the traditions of wooden housing construction are rooted in the distant past. And this is not the only direction of its application. Furniture and household items made of wood have long become interior classics. But everything is changing, a person is actively mastering new technologies and materials, and in the field of construction and furniture production, materials based on wood fibers and chips have appeared - these are various composites of wood and its derivatives: fibers, chips and veneer. Fiberboard (Fiberboard) - what is it? Dimensions, sheet thickness and price of fiberboard are the subject of our today's review. Let's start.
How did it all begin? It should be noted that before the advent of wood composites, the yield of solid wood products at best was only 40%, the remaining 60% of the wood went to waste. Today, the amount of waste is only 10-12%, largely due to the emergence of composite materials, the basis of which is wood waste from the main production. It is not for nothing that the Germans are considered a thrifty nation, it was in Germany, in the 1930s, that particleboard appeared - chipboard, more often it is called particleboard.
It was based on production waste: wood chips and shavings impregnated with phenolic resins. The first samples of composites were rather fragile, had a number of drawbacks, in addition, they were somewhat poisonous, since a binder based on phenolic resins released harmful substances into the atmosphere. Today we managed to get rid of these problems. Modern composites are durable, moisture resistant and absolutely harmless to humans: either chipboard or fiberboard. This also applies to all materials based on them.
Good to know! There are particle boards (particle boards) such as delta wood or bakelite plywood. The official name of the particle board is particle board. Nevertheless, the name chipboard in speech most often means chipboard products.
Not everyone knows what features the fiberboard material has. What kind of raw material is it, how it is produced and where it is used, we will try to find out further.
Fiberboard is sheet material made by hot pressing of wood fiber base impregnated with binder resins. It is used in construction, in the decoration of residential premises, in and in industrial production. The field of application of composite materials based on wood fiber is wide, and it cannot be covered in one article. Fiberboard is found in any modern room, it can be a sheet laid on the floor as a substrate for a laminate, wall decoration for summer cottages and back walls of cabinets in your apartment.

Types and varieties of fiberboard
Depending on the production technology, the amount of binder and the type of wood, different physical parameters of the fiberboard can be obtained. Let's look at an example.
If you need to buy fiberboard, the price for a sheet of fiberboard of the same size varies greatly and depends on the brand of the product, its quality and characteristics. The types of fiberboard products are classified according to GOST 27935-88, but often transliterations of foreign names LDF and MDF are used to designate certain types and varieties, for example. It is worth noting separately that slabs can have two quality categories - A and B, depending on the surface treatment, they are divided into two grades, denoted by Latin numbers.
All the main characteristics of fiberboard are indicated in its labeling. These are the type, dimensions of the slab, its thickness, quality category and grade.
Soft fiberboard: features and characteristics
A characteristic difference between soft fiberboard varieties from the rest is the almost complete absence of chemical resin binders in them, the binder in this case is a natural material - lignin, which is contained in large quantities in the resin of coniferous trees. For this reason, coniferous trees are used for the manufacture of soft varieties of fiberboard composites, since hardwood does not contain significant amounts of this substance.
The characteristic features of soft chipboard are porosity and low density of the material, which imposes certain conditions on its use. You can buy soft fiberboard for noise and heat insulation of residential premises, as a lining under the roof or floor of the house. Use this grade of fibreboard for exterior decoration not recommended, these boards have low moisture resistance.
Soft fiberboard is produced in several grades, differing in the presence and amount of the binder. Soft types are marked - M-1, M-2 and M-3. The thickness of the slabs ranges from 6 to 16 mm.

Important! This brand of fiberboard is absolutely safe in terms of ecology! Soft varieties are made only from wet carpet and softwood. There are no chemical additions in soft fiberboard.
Semi-solid fiberboard: features and scope
Semi-solid grades, this is a medium density fiberboard composite, from 400 to 800 kg / m3 produced by the wet method, this material is used most often for the manufacture of back walls of cabinets, drawers and countertops.
It should not be confused with other types of composites, with low density fiber composite - LDF, which are produced by dry pressing and have completely different parameters, including a higher density. And MDF panels, which are also referred to as medium density wood fiber composites, but have significant differences in production technology, structure and mechanical characteristics. Semisolid slabs are marked with the letters NT.
Hard fiberboard: marking and use
According to GOST 27935-88, hard fiberboard is a pressed fiberboard with a density of over 800 kg / m3. Classification of hard fiberboard types is made according to GOST 4598-86:
- T - an ordinary plate, without additional grinding of the front surface. Ideal for use as a building material or substrate;
- TS - with a coating of the front surface with finely dispersed wood pulp, these boards are distinguished by increased resistance to mechanical stress and abrasion. Mostly used in the manufacture of furniture;
- T-SP - coating the surface of the slab with tinted fine wood pulp. These plates are simply necessary if, for example, you need to buy white fiberboard;
- T-B - non-refined surface, increased moisture resistance, building material and production of packing boxes;
- T-SV - front surface coating, increased moisture resistance, furniture production and finishing work in places with high humidity.
The thickness of the sheets in this case: 2.5 mm, 3.2 mm, 4.0 mm, 5.0 mm, 6.0 mm, the dimensions are regulated by GOST 4598-86, the maximum size of hard plates: 1.70x5.50 m and 2.14x6.10 m, but more often standard ones are used, the derived dimensions of the slabs to which we will refer below.

Superhard fiberboard: features and application
This type of fiberboard is a high density solid board from 950 kg / m3. The high hardness of the slabs is achieved by introducing pectol or other compounds that strengthen the material into the composition. Superhard grades of fiberboard are used for the manufacture of furniture, and as a building material. Including for interior decoration, floors, walls, production of partitions, doors and arches. They are also produced with various finishes of the front surface, there is both a non-refined surface and an imitation of a wood texture or a plastic coating with a decorative pattern.
Laminated fiberboard - a special subspecies of finishing material
One of the varieties of hard fibreboard, characterized by a refined surface. In this case, the surface of the slab is covered with an even layer of synthetic material, which levels the panel and gives it a pleasant appearance, resistant to external factors. There are the following types of LDL:
- Tiled LDVP, in this case, the product looks like a tile with a front surface covered with plastic, the size of the tile varies from 0.3x0.3 meters to large panels measuring one meter by one meter. The panels are fastened by the thorn-groove system;
- Lining - laminated fiberboard, everything is clear from the name, this material is used to decorate walls and ceilings;
- Sheet laminated fiberboard, used mainly for finishing horizontal and vertical surfaces.
The peculiarities of this material are high soundproofing characteristics and ease of hygienic processing of such surfaces, the use of these panels for interior decoration in some cases is just a panacea! Especially considering that you can buy laminated fiberboard at a relatively low price. Although wall and ceiling panels have a competitor, PVC honeycomb panels, wood fiber panels are still in price.

Keep in mind that when buying laminated fiberboard, the sheet size and prices may vary from manufacturer to manufacturer, so there is always an opportunity to save a little budget. But at the same time, it must be borne in mind that it is not worth purchasing building materials from an unknown manufacturer, pay attention to the certified goods of more or less well-known brands. This guarantees the quality of workmanship, environmental safety and a long service life of such products.
Fiberboard and particleboard - the difference is only in the name?
There are a lot of wood composites on the material market. First you need to find out: what is the difference between fiberboard and chipboard, what is the difference between them from a wood-layer composite or from oriented strand boards.
First of all, the difference between these types lies in the material for manufacture, production technology and mechanical parameters. There seems to be little difference, wood is used in all types of these products. But, in the production of fiberboard, fiber is used, in contrast to the chips and shavings that make up the particleboard. Fiberboard or particleboard - which is better? Let's look at some examples.
A larger gradation of the constituent elements affects the cost, a chipboard sheet is cheaper than a fiberboard composite sheet, but at the same time, the characteristics of fiberboard materials are much superior to those of chipboard. So, for example, chipboard is difficult to process, it begins to crumble when screws are screwed into it, it is less resistant to moisture due to the heterogeneity of the structure.
In addition, chipboard has a large weight, and a large thickness, all other things being equal, this is largely due to the material used for manufacturing. Fiberboard is free from these disadvantages, but at the same time, with the same parameters, it has a higher price.
So it turns out that each material is good in its place, somewhere it is better to use chipboard sheets, if the structure is not loaded, and is located in a dry place, and somewhere you will have to use a fibrous web, due to the load and high humidity. OSB, oriented strand board, is practically analogous to chipboard, but with a higher strength.
But there is also such a composite material as plywood. The question that many craftsmen ask: is plywood chipboard or fiberboard? Neither one nor the other. In this case, veneer serves as the main material - thin layers of wood that are collected in a bag, glued with resins and pressed, in other words, plywood is a separate type of wood composite.

Related article:
One of the most reliable and durable building materials, characterized by high strength and affordable price. The advantages and disadvantages, selection criteria and features of laying grooved chipboard - in our material.
Scope of application of wood fiber materials
The use of fiberboard largely depends on its mechanical characteristics, sheet dimensions. The thickness of the fiberboard sheet also plays a role. So, relatively thick sheets of soft fiberboard are good to use as a building material, for insulation, etc. Medium hard fiberboard, LDF and MDF panels have occupied their niche in the interior decoration of premises. Hard and superhard varieties are actively used in construction and furniture manufacturing.
The variety of tasks and the breadth of the field of application is reflected in the range of products. The dimensions of the fiberboard sheet, the width and length of the panel depend on the manufacturer and on the needs of the buyer. Although the state standard provides for the standard sizes of the production of fiberboard sheets, at the same time, the range of products made of fiberboard contains finished finishing elements: tiles, panels and lining.
One of the main uses of fiberboard is finishing. It is worth considering in more detail the features of the use of this material.

Wall decoration
For finishing work on vertical surfaces, laminated fiberboards are mainly used, this is due to both the convenience of working with them, the pleasant appearance of such a finish and the ease of further maintenance of the plastic-coated surface. The advantages of this type of finish:
- No additional preparation of the wall is required, since the panels are installed on a frame made of a metal profile or a wooden bar;
- For the production of work, no special skills and special tools are required, since fiberboard panels for walls for interior decoration have a pinch-groove fixation system, which facilitates their docking, fastening to the frame is carried out by means of special clamps;
- The fiberboard wall panel is produced in a ready-made version, with a pattern or imitation of the texture of wood and does not require additional finishing work;
- Smooth surfaced fibreboard can be used for wall cladding, in which case any desired coating can be applied over it. Pasting wallpaper on fiberboard, although a rather laborious and time-consuming process, will not cause any difficulties when dismantling the old coating, unlike similar works with finishing from.
It is worth noting a large assortment of wood composite panels of various sizes and appearance.

Floor finishing
The floors are the most loaded element of the room, therefore, the use of sheet composites, which have a relatively low strength, should be evaluated in each case. It is easy to lay fiberboard on the floor, but it is difficult to redo the floor again. Basically, fiberboard is used when laying the floor on an already existing plank covering, less often on logs. In the first case, the floor is leveled with fiberboard sheets, in the second, the floor is leveled with lags, but in this case it must be borne in mind that the loads on the floor should be small. Often, fiberboard panels are used as a gasket, for example, you can lay fiberboard under linoleum on a wooden floor.

But what is better for the floor (fiberboard or particleboard), there is no consensus on this question. Particleboard in this case has some advantages, as a denser and thicker material, less subject to deformation from load. For rough flooring, it is better suited than fiberboard. It is better to lay the fibreboard on the old floor.
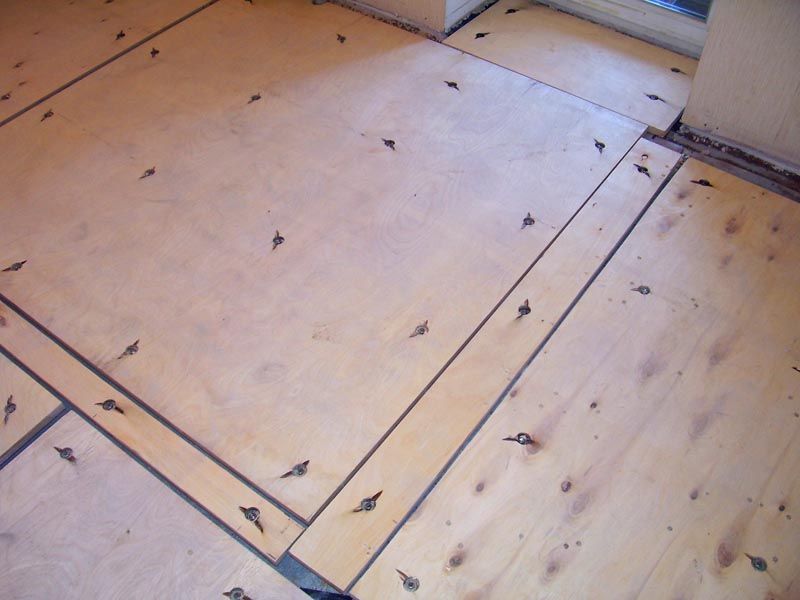
Ceiling decoration
For finishing the ceiling, you can use both sheet fiberboard in its pure form for finishing, and laminated panels. In the first case, rough finishing of the ceiling is possible, for example, with soft fiberboard. This will improve sound insulation and insulate the ceiling if necessary. In addition, this grade of fiberboard is more breathable. The use of fiberboard for ceiling decoration has the following advantages:
- Simplicity of the device and installation of the fiberboard ceiling;
- Environmental friendliness;
- Moisture resistance, but at the same time direct ingress of water Fiberboard panels contraindicated;
- Water vapor permeability.
In the case of using fiberboard as a rough material, the sheets can be painted quite easily or ceiling tiles can be glued onto them. But then a quite reasonable question arises: how to paint the fiberboard? Any paint, since the surface of the fiberboard is sufficiently resistant to the effects of chemical dyes, and you can paint with alkyd, oil, acrylic paint and even nitro enamels.

The range of wood fiber products is extremely wide. Buy fiberboard sheets or ready-made ceiling panels - here the choice of option is yours.
The use of fiberboard in everyday life
Fiber boards are used not only for construction, they can be used for assembling furniture, arranging doors and various kinds of partitions. Lightweight and durable material is needed in everyday life. Especially considering the large area of \u200b\u200bfiberboard sheets.

So, for example, fiberboard can be used to create a bee hive. In this case, the wooden frame needs to be sheathed with sheets, the gaps between which should be filled with insulation. Homemade beehives made of fiberboard will significantly outperform traditional bee nurseries made of wood in terms of weight and cost, which is important on an apiary scale.

Features of working with fiberboard
How to process chipboard, how to fix it and how to cut it - these are the main questions that have plagued the craftsmen of the planer and hammer for quite some time. For example, few people know how to stick fiberboard on fiberboard, because even liquid nails and epoxy adhesives do not always cope with this task. In this case, ordinary construction PVA glue or special adhesives for gluing fiberboard can help.
How to cut fiberboard at home? Again, it's very simple - with an assembly knife or a hacksaw for metal. It is worth paying attention to the knife cutting technology. The knife blade must be sharp, it is best to cut with a metal ruler and slowly and carefully, otherwise there is a possibility of damaging your fingers when the blade breaks off. There are also several roller-type devices for cutting fiberboard, one of which is shown in the photo.

Frequent question and surface finish of fiberboard. Wallpapering or painting. The fact is that fiberboard does not accept moisture very well and has low adhesion. In other words, paint sticks poorly to the fiberboard surface. For this reason, the surface must be primed before painting. For convenience, you can prime the sheets before mounting them on the frame.
A separate issue with the preparation of the fiberboard surface for wallpapering, since this material does not tolerate moisture well, then before applying wallpaper glue, which can cause warping of the panels, it is worth painting the surface. Then further finishing will not raise questions or problems. Here is the answer to the question whether it is possible to glue wallpaper on fiberboard. You can, but you need to prepare the surface.
Often, during the operation of fiberboard products, defects appear on them, this can be both mechanical damage and traces of operation. Traces of exploitation in the form of dents and scratches are easy to repair. To do this, you just need to putty the damaged surface, then paint it, or cover the surface with a self-adhesive film.

In the case of the formation of a through hole in the floor or in the door made of fiberboard, such situations also sometimes arise, first of all it is necessary to prepare materials for the repair, first of all, it is a sharp assembly knife, putty, a piece of fiberboard, polyurethane foam and any filler.
Before sealing the hole in the fiberboard door, cut off the uneven and dented edges of the hole, so that the edges of the hole are even, without dents or cracks. Then we install it inside the hole, it can be fixed bars, pieces of fiberboard or crumpled, thick paper. The next step is to fill the hole with foam, after it has hardened, it is necessary to cut off the protruding foam flush with the door surface.
After that, the surface of the door around the hole and the foam is putty, for example, with epoxy resin. After drying, everything is again cleaned with fine sandpaper, which is best fixed on a wooden block. This will ensure a level surface. Then you need to restore the appearance of the door itself, this can be done either by painting, or by sticking a self-adhesive film with imitation of wood texture, or veneering.

If there is a through hole on any base, most often this happens when fiberboard is laid on a wooden floor, a bulging board can wipe the sheet through. In this case, it is best to change the entire sheet, in parallel with this, deal with the board, process it with a plane or fix it with self-tapping screws. But often this is not possible, so you can proceed as follows. Carefully, using a mounting knife, cut off the wiped hole until you get an even geometric figure. Then cut out a patch of the same size from a piece of fiberboard and insert it into the resulting socket, securing it there with self-tapping screws or glue.
Thus, despite some features in the processing of fiberboard, the material is quite subject to handmade and home repair.

Dimensions, thickness and price of fiberboard sheets
Most clearly, the calculation of the size, type and price of fiberboard can be made using the example of building an inexpensive turnkey bath, with interior decoration Fiberboard sheets.

It is worth considering that sheathing the surface of the bath from the inside is possible only with MDF panels, since they are most resistant to moisture, while for insulation, you can use soft fiberboard sheets, M-1 and M-2, 10-12 mm thick. They can be used to tamp the walls and ceilings of changing rooms and lounges. This will help reduce the construction budget somewhat. Insulation of humid areas is best done with foam or foil insulation.
The calculation of the required materials is carried out using the simplest linear formulas, the length and width of the area covered by the sheet, taking into account the cutting. After evaluating all the factors, you can determine the required type of fiberboard, size and thickness of sheets, prices. The photos will more clearly show how wood composites are used - panels in the decoration of the bath.

Standard sizes of fiberboard sheet: how to take them into account when cutting
Fiberboard production is strictly regulated by GOST 4598-86 standards. According to him, the slabs have the following dimensions:
- Hard grades of fiberboard:
- length - 1220, 1700, 1800, 2050, 2500, 2745, 3050, 3350 and 3660 mm, maximum 5500 and 6100 mm;
- width - 610, 1220, 1525, 1700, 1830 and 2410 mm;
- Soft grades of fibreboard:
- length - 1220, 1600, 1800, 2500, 2700 and 3000 mm, maximum 5500 mm;
- width - 1220 mm.
When producing slabs, slight deviations within 3-5 mm are allowed. In addition, GOST makes it possible, in agreement with the consumer, to produce slabs of non-standard sizes, taking into account the possibility of waste-free cutting. Variations in sizes are possible up to the maximum sheet size specified in the state standard.
Thus, the dimensions of the standard format fiberboard can be different. Usually, the main dimensions of the slab are indicated in the product labeling. The size of the slab is selected based on the purpose and place of application of the fiberboard. The size of the sheet can be any, the main thing is to achieve a minimum amount of waste when cutting.
Standard thicknesses of hard and superhard boards, as well as semi-hard boards equivalent to them: 2.5 mm, 3.2 mm, 4.0 mm, 5.0 mm, 6.0 mm. Thickness of soft slabs: 8.0 mm, 12.0 mm, 16.0 mm. The thickness of the fiberboard sheet is also selected based on the conditions of use.
When cutting, it is necessary to calculate the sheets so that they cover the maximum calculated area, with a minimum amount of waste. This will significantly reduce the budget for the purchase of material.

Fiberboard price per sheet and what it depends on
So how much is a fiberboard sheet? The price of a stove is made up of a number of constituent factors - the cost of manufacturing, delivery to the end consumer and the seller's margin. The cost of making a sheet is primarily influenced by the popularity of the manufacturer, the cost of components used in its production. The cost of the binder is especially important in this case. As you know, high-quality components and are not cheap, it is for this reason that when purchasing building materials you should focus on the average price category, in the case of an expensive one, there is a high probability of overpaying for a well-known brand, in case of an unnecessarily low price, you will receive products made of substandard materials and not corresponding to the passport characteristics ... But, one should not confuse substandard products in terms of quality with substandard products in appearance, these are two completely different concepts.
No less important price parameters are the overall dimensions of the sheet and its thickness. So the price of a fiberboard sheet (dimensions in this case do not matter) of an unrefined and laminated panel will significantly increase towards the latter, only due to the surface treatment with plastic.
So how much does a fiberboard sheet cost? The average cost is from 160 rubles and more per sheet with dimensions of 2.5x1220x2440 mm.
The cost of laminated board represents a different order of prices, due to the introduction of additional components for processing the front side of the panel. The average price for a sheet of laminated fiberboard is from 300 rubles.
To purchase the required number of sheets of fiberboard, first of all, it is necessary to accurately assess the scale of the work, choose the required dimensions and thickness. Determine the required varieties and area of \u200b\u200bfibreboard.
To acquire construction Materials, including fiberboard, is in large hardware stores, in this case there is a guarantee that the products were transported and stored in conditions that allowed it to keep their specifications, and did not lie for weeks in the rain and damp, as is often the case in the construction markets.

Important! When buying fiberboard panels, please note that substandard products, with broken edges, non-critical damage. The cost of fiberboard sheets with damage, or substandard type, is always lower than the average price in the store. In addition, the stores often sell cuttings of slabs, if necessary, you can purchase them, these simple steps will help to significantly reduce the burden on the budget.
Thus, it can be seen that fibreboard products have occupied their niche in construction and furniture production, a niche limited by the physical characteristics of the material, but, nevertheless, fibreboard is quite consistent with it in terms of price and performance.

Windproof plates
By adding rosin and paraffin to the wood pulp, the resistance of porous fiberboard boards to weather conditions is increased. The boards processed in this way can be used as windbreak boards in external framing walls. In addition, they add additional rigidity to the wall structure.
Fiberboard windproof boards are available in 12 and 25 mm thicknesses. Standard size of windbreak plates: 1200 x 2700/3000 mm. Due to their strength and insulating qualities, the 25 mm thick windproof boards are well suited for use in vertical frame structures.
Due to its low thermal conductivity, the windshield plate forms a barrier that prevents the penetration of cold inside and, thus, improves the thermal insulation properties of the structure.
In addition to being used in external walls, wind protection boards are suitable for thermal insulation of upper floors. When insulating the bevels under the roof of a building by spraying wood fiber wool, it is recommended to sheathe the inner surfaces of the outer walls and roof with windshield plates.
Weatherproof windshield boards are also well suited for cladding under load-bearing floor slabs and underground, before filling them with insulating material.
INTERIOR FINISH OF ROOMS
Fiberboard boards suitable for interior decoration:
- all standard MDF boards
- fiberboard boards with additional cladding, intended for interior decoration
What is important to consider when facing with fiberboard plates:
- Fiberboard plates are well suited for interior decoration of country houses. The boards are not recommended to be used in rooms with high humidity, and as a basis for laying ceramic tiles.
- In dry rooms, changes in the shape of the slabs due to exposure to moisture are insignificant. Swelling in the joints of porous slabs, appearing due to their too dense installation, can be smoothed out. This produces a smooth, even wall.
- Porous fiberboard and hardboard with drilled holes also serve well as sound insulating material for rooms.
Untreated standard fiberboard
The porous fiberboard (untreated standard board) is used for cladding the inner surfaces of walls and ceilings, and also as an additional insulating layer inside the structure of external walls. For cladding, 12 mm boards are used in one or two layers, or 22 mm boards in one layer. If the slabs are fastened in two layers, the joints of the slabs of different layers should be in different places. According to the degree of surface treatment, untreated fiberboard boards belong to class E.
Fibreboard boards for the needs of the industry and products from them
In the industry (especially furniture and in the production of doors), mainly solid fiberboard (hardboard) boards are used, as well as products from it with different facing.
Painted solid fiberboard is used for the needs of joinery and furniture production. They are also used in exhibition structures and interior decoration. Painted solid fiberboard boards are produced standard sizes - 1220 x 2440/2745/3050 mm and thickness 3.0 mm, 4.8 mm or 6.0 mm.
Fiberboard boards are faced with natural wood veneer, paper, fabric, plastic, fiberglass, metal and cork.
Other products made from fiberboard panels have a precise final purpose and are produced by finishing the front side of standard fiberboard panels with various coatings or by additional processing of the panels. For example, hard fiberboard boards are produced to order in a painted form, as well as with exact dimensions, with oil impregnation, with various types of facing and with perforations.
MDF (medium density fibreboard) boards are made from wood fibers by pressing with glue. The glue content varies depending on the type of product. MDF boards differ from other types of fibreboard in the way they are made, as well as in the content of glue. In the manufacture of MDF boards, finer fibers are used. Basically, MDF boards are used in the production of furniture, and on their basis, many names of other sheet and panel products for interior spaces with veneer coating or painting are produced.
FIELD OF APPLICATION OF FIBER PLATES
Building
- wind protection under the roof and sheathing under the lower ceilings and underground for laying additional thermal insulation
- inner lining
- additional thermal insulation
- concrete formwork and other temporary structures (for example, construction site fences, protective structures)
Construction industry
- central part of I-beams
- rear walls of built-in furniture
- window frame surface material
Vehicles
- car interior trim
Other applications
- packaging
- exhibition structures
RUB 749.00 / Sheet
Fiberboard (Fibreboard)Fiberboard (Fibreboard) or hardboard - are called sheet materials formed from wood fibers. They are made from wood waste or low-quality round wood. In some cases, depending on the conditions for supplying the enterprise with raw materials, both wood waste and low-grade wood in round form are used simultaneously.
Fiberboard is widely used in construction and furniture production. It is used as heat and sound insulation for roofs, floor ceilings, wall partitions, and also as finishing material for walls. Hardboard is often used as a bedding for laminate and parquet to level the floor surface. In the furniture industry, this material is used as the back walls of cabinets and drawer bottoms, as well as for the manufacture of inexpensive interior doors. In artistic creation, a hardboard sheet replaces canvas and paper.
Unlike chipboard (chipboard) made from shavings and small waste woodworking, fiberboard is made from cellulose fibers, making the hardboard furniture becomes flexible.
Fiberboard is produced in two ways:
- Wet pressing of wood fibers without binder. The raw materials adhere to each other thanks to the natural lignin in the fibers. A metal mesh is used as a press: the plate is smooth on one side, and mesh on the other. Hardboard produced in this way does not contain synthetic resins and is completely environmentally friendly, but not strong enough and moisture resistant;
- Dry pressing of fibers mixed with adhesive. Such hardboard is characterized by rigidity, strength and moisture resistance, but it cannot be considered environmentally friendly.
Advantages of fiberboard:
- Moisture resistance: this material can be used in rooms where high humidity is constantly observed (for example, toilet, bathroom or kitchen).
- Heat and sound insulation: very often, fiberboard is used as an insulating material, so such a ceiling will not only keep the house warm, but also protect from external noise.
- Material cost: Fiberboard is very inexpensive, so everyone can buy it.
- Water vapor permeability: such a surface allows air to pass through well, promoting its circulation inside the room.
- The weight: such material is lightweight, so the fiberboard ceiling will practically not create additional load on the main floor.
Disadvantages of fiberboard ceilings:
- Moisture resistance: although fiberboard can be used in a bathroom or toilet, it will not withstand direct exposure to water. Therefore, when flooding from above, the hardboard surface will be damaged.
- Environmental friendliness: this point applies to old fibreboard, bought a long time ago and stored somewhere in your garage or in a closet at your dacha. It is highly discouraged to use them, because earlier, at the stage of manufacturing the material for gluing the fibers, not entirely safe substances were used, which over time were released into the surrounding space. Therefore, after finishing the surface with such plates, there will be a specific and very unpleasant smell in the room. Now the technology for manufacturing fiberboard has changed a lot, and there are no such harmful components in modern materials, so they can be safely used in residential premises.
- Design: for example, a ceiling finished only with fiberboard is unlikely to suit anyone, therefore it serves to form an inner layer leveling the surface, on top of which a decorative ceiling covering will be applied (for example, from plastic tiles, wallpaper, paint or other finishing materials).
- Labor intensity: despite the fact that the material itself is very light and it will not be difficult to lift it, it will be quite difficult to sheathe the surface with it alone. The sheets are very flexible, therefore, during installation, they must not only be aligned with other elements, but also be constantly monitored so that they do not sag, otherwise the surface will end up wavy.
SPECIFICATIONS
There are three types of fiberboard: soft (the brand is designated by the letter "M"), hard ("T") and superhard ("ST"). The most common brand of fiberboard is TSN-40 - a solid board of high strength.
Hard fiber boards, depending on the strength and type of front surface, are divided into grades:
T - Hard fiberboard boards with non-refined front surface;
Т-С - hard fiberboard boards with a face layer of finely dispersed wood pulp;
T-P - hard fiberboard boards with a tinted face layer;
T-SP - hard fiberboard boards with a tinted front layer of finely dispersed wood pulp;
ST - high strength solid fiber boards (superhard) with an unrefined front surface;
ST-S - high-strength (super-hard) hard fibreboards with a front layer of finely dispersed wood pulp.
Hard fiberboard boards of grades T, T-C, T-P, T-SP, depending on the level of physical and mechanical indicators, are divided into quality groups: A and B.
M-1, M-2 and M-3 - Soft plates depending on their density.
Fiberboard application:
- In construction (external and internal elements, agricultural buildings);
- For the manufacture of built-in furniture (kitchen cabinets);
- In furniture production;
- Automotive and shipbuilding;
- In the production of containers, boxes, etc.
Fiberboard types depending on the purpose:
Superhard, hard and semi-hard, soft, insulating and insulating finishing.
Superhard fibreboards are very dense. Their density is 950 kg / m3. They have their own marking ST-500. These boards are made by wet fiberboard production. During the production process, only the front side of the slab is painted and primed. Superhard fiberboard is obtained by impregnating the starting material with a by-product of processing - pectol. Thanks to its use, the strength of the fiberboard increases by 20%. Such fiberboard is most often used for covering floors, it is also widely used in building structures and products - partitions, floors, temporary structures, doors, containers, etc.
Solid Fiberboard is available with a density of 800-1000 kg / m3 and a thickness of 2.5-6 mm. Depending on the density, strength and type of front surface, they have different markings. Grade "T" is a fiberboard with an unfinished front surface; "TS" - has a finely dispersed front layer of wood pulp; "NT" - low density fiberboard. Fiberboard plates of the TC and T grades, depending on the quality of the surface of the plate, are divided into I and II grade. Solid slabs are used for the manufacture of back walls of furniture, panel doors, etc.
Average density semi-solid fibreboards not less than 850 kg / m3 and thickness 6-12 mm. Most often, back walls of furniture, drawers, etc. are made of these plates.
In a separate group there are soft fibreboards. They have a low density of 150-350 kg / m3 and a thickness of 9-25 mm. They are made by drying the carpet without the use of hot pressing. Soft fiberboard is characterized by low thermal conductivity, high density, but low strength. Low strength greatly limits the scope of application.
Fiberboard is used as thermal insulation material... Soft fiberboard is used as a heat-insulating material in different areas, depending on the brand. So, fiberboard treated with latex is used for roof insulation. Also, the soft board is used for sound and thermal wall decoration. It is used in all multi-layer structures of floors and walls in residential premises, in interfloor ceilings, etc.
Refined fibreboard (DVPO) is used as finishing material for ceilings, walls, for the manufacture of doors, furniture. In the manufacture of DVPO, the technology of applying a multilayer coating to the front surface is used. At the first stage, a primer layer is applied, which creates a background part on the coating. Then a pattern is printed that simulates the structure of wood. Refined fiberboard is highly resistant to moisture and abrasion. To protect the coating from mechanical stress, scratches, varnish is applied on top of the DVPO.
The integrated use of wood is aimed at increasing the economic efficiency of the forestry and woodworking industry by reducing logging and at the same time fully using wood waste and low-grade wood as technological raw materials.
Fiberboard, or abbreviated fiberboard, is a sheet material that is made in the process of hot pressing of wood fibers and shavings, with the addition of various binding additives to the mixture. Typically, additives contain polymer-based resins. In addition to additives, they include additional components that improve the waterproofing properties of fiberboard. These substances include water repellents (ceresin, paraffin), antiseptics, etc.
Fiberboard is produced traditionally in two ways - dry and wet. But not so long ago, two more intermediate methods for the manufacture of fiberboard appeared - wet-dry and semi-dry.
1. In the process of making wood fiber boards by dry method, the carpet is formed directly in the air, and then hot pressing and cutting into webs takes place. The process of forming a fiberboard carpet takes place at higher temperatures than in the wet method, but the pressure is lower.
As a result, low pressure fiberboard plates are obtained, which have a more porous and loose structure. Humidity during production is not high 6-8%.
2. The wet method provides for the formation of a special carpet from the dried wood fiber mass in water and pressing under heating. And only then the sheets are cut into separate canvases. The humidity of the canvases is 60-70%.
3. The production of fiberboard in the semi-dry method follows the dry method scheme. Only humidity changes, it is about 16-18%.
4. In the wet dry method, a wood fiber carpet is formed in water, and then the carpet is dried and the dry material is hot pressed. The relative humidity of the production is practically zero.
With any of the above-described method for the production of fiberboard, the raw material is finely frayed, while the wood turns into fibers, from which a fiberboard carpet is formed.
Distinguish fiberboard plates on superhard, hard and semi-hard, soft, insulating and insulating finishing.
Superhard fiberboards are very dense. Their density is 950 kg / m3. They have their own marking ST-500. These boards are made by wet fiberboard production. During the production process, only the front side of the slab is painted and primed. Superhard fiberboard is obtained by impregnating the starting material with a by-product of processing - pectol. Thanks to its use, the strength of the fiberboard increases by 20%. Such fiberboard is most often used to cover floors; it is also widely used in building structures and products - partitions, floors, temporary structures, doors, containers, etc.
Hard fiberboard is available with a density of 800-1000 kg / m3 and a thickness of 2.5-6 mm. Depending on the density, strength and type of front surface, they have different markings. Grade "T" is a fiberboard with an unfinished front surface; "TS" - has a finely dispersed front layer of wood pulp; "NT" - low density fiberboard. Fiberboard plates of the TC and T grades, depending on the quality of the surface of the plate, are divided into I and II grade. Solid slabs are used for the manufacture of back walls of furniture, panel doors, etc.
The average density of semi-solid fibreboard is not less than 850 kg / m3 and a thickness of 6-12 mm. Most often, back walls of furniture, drawers, etc. are made of these plates.
In a separate group, there are soft fiber boards. They have a low density of 150-350 kg / m3 and a thickness of 9-25 mm. They are made by drying the carpet without using hot pressing. Soft fiberboard is characterized by low thermal conductivity, high density, but low strength. Low strength greatly limits the scope of application. Fiberboard is used as an insulating material. Soft fiberboard, as a heat-insulating material, is used in different areas, depending on the brand. So, fiberboard treated with latex is used for roof insulation. Also, the soft board is used for sound and thermal wall decoration. It is used in all multi-layer structures of floors and walls in residential premises, in interfloor ceilings, etc.
Refined wood fiber board (DVPO) is used as a finishing material for ceilings, walls, for the manufacture of doors, furniture. In the manufacture of DVPO, the technology of applying a multilayer coating to the front surface is used. At the first stage, a primer layer is applied, which creates a background part on the coating. Then a pattern is printed that simulates the structure of wood. Refined fiberboard is highly resistant to moisture and abrasion. To protect the coating from mechanical stress, scratches, varnish is applied on top of the DVPO.
Depending on the operating conditions, fiberboard plates can last from 30 to 35 years.